The core technology that have driven the development
of NEGAMI are Suspension polymerization in water.
This is one of procedure used to induce radical polymerization with a vinyl group monomer. A polymerization process in which a insoluble monomer is dispersed and suspended by continuous strong agitation in a liquid phase, usually water, and it become monomer droplet with the size of 0.01~1mm. In addition, the polymerization in which soluble initiator(for example:benzoyl peroxide or azobisisobutyronitrile) is added in the monomer. Polyaddition reaction such as polyurethane may also performed in a suspended form .
Polymerization advances in the droplet of a monomer and particle polymer is obtained. Spherical particles are obtained by performing suspension polymerization with the use of vinyl acetate, styrene and methyl methacrylate etc. as a moner, in this case, it is called pearl polymerization. Polymerization within droplet is essentially the same as bulk polymerization, and polymerization rate and degree are high. In suspension polymerization, if polymerization advances, monomer droplet will serve as thick solution of the polymer which uses a monomer as a solvent, and droplets will stick easily. Therefore,it needs to perform by constant strong agitation and add water soluble polymer such as gelatin, starch, polyvinyl alcohol and carboxymethylcellulose, and insoluble powder such as calcium carbonate and magnesium carbonate to stabilize droplets.
Generated polymer particle size also changes with agitating speed. As the heat released during the polymerization is absorbed by the surrounding solvent, selective heating does not happen and it is easy to adjust temperature.
Suspension polymerization most commonly used as industrial manufacturing method in order to get polymer for forming material such as polystyrene, polymethylmethacrylate, polyvinyl acetate, polyvinyl chloride, because a polymer with a high degree polymerization is obtained with the polymerization and generated polymer isolation is easy.

This is one of procedure used to induce radical polymerization with a vinyl group monomer. Emulsion or surfactant are dissolved in waterand water insoluble or poorly water-soluble monomer is added in it. It is the method of performing polymerization by using soluble initiator(for example:benzoyl peroxide or azobisisobutyronitrile).
In the water solution of surfactant above a specified level, surfactant molecules associate to form a micelle. Surfactant is comprised of hydrophilic and hydrophobic, and associate with hydrophilic for exterior,in other words, water side. If a monomer is added into aqueous solution in which the surfactant froms micelle, since a monomer is water-insoluble,it is taken in part into micelle and exist in it as droplet. Polymerization initiator used with Emulsion polymerization is water-soluble and starts polymerization as generated radical in water phase reaches monomers in a micelle.
Emulsion polymerization is totally different from Bulk polymerization and Suspension polymerization used in other radical polymerization in this point. Radical responsible for polymerization is only one in micelle and polymerization does not stop until the next radical enters into micelle from water phase. Moreover, if the monomer in micelle is consumed, monomer will be reinforced from underwater monomer droplet and polymerization will continue advancing. Therefore, polymer with high degree polymerization is obtained rather than obtained by bulk polymerization or suspension polymerization. As the heat released by the polymerization is absorbed by water around micelle in Emulsion polymerization, so it is easy to adjust temperature like Suspension polymerization. generated polymer obtained in Emulsion polymerization is used for various purposes such as paint, textile treating agent and adhesive without any change. Although salts are added, it can condense and solidify and polymer can also be produced commercially, but a surfactant remains easily.
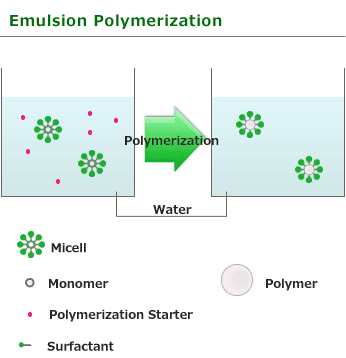
This is one of procedure used to induce radical polymerization with a vinyl group monomer. It is a type of polymerize by heating and using monomer and initiator. Benzoyl peroxide and azobisisobutyronitrile soluble in monomers or solvents is used for initiator.
The feature of solution polymerization is that the polymerization degree and rate is reduced compared with Bulk polymerization. As the heat released by the reaction is absorbed by the solvent, so it is easy to adjust temperature.
Solution polymerization is quite useful for the use as polymer fluid as it is after polymerization but need to remove solvent and collect polymer to take polymer as solid form.
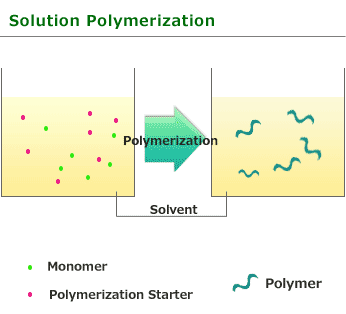
This is one of procedure used to induce radical polymerization with a vinyl group monomer. It is carried out by adding only vinyl monomer without solvent usage or a small amount of initiator.It is a type of polymerize by heating. Benzoyl peroxide and azobisisobutyronitrile soluble in monomers is used for initiator.
The feature of bulk polymerization is that the polymerization rate is high and relatively-pure polymer is obtained with Bulk polymerization. As the removal of heat of polymerization is difficult,it is hard to adjust temperature with selective heating.In addition,post-processing is complicated for example generated polymer become solidified and it is attached to the container.
Industrially,bulk polymerization is used for fabrication of polystyrene pellet by the continuation bulk polymerization from styrene monomer, production of the organic glass of polymethylmethacrylate, hardening of glass-fiber-reinforced unsaturated polyester, polymerization-fabrication (casting polymerization) in a metallic mold, etc.
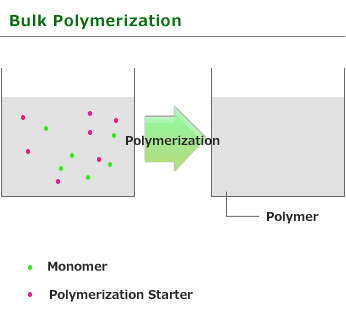
This is one of procedure used to induce radical polymerization with a vinyl group monomer. It is a type of polymerize by heating and using solvent which does not swell easily with soluble monomer and initiator(in addition,generated polymer is not dissolved). Benzoyl peroxide and azobisisobutyronitrile soluble in monomers or solvents is used for initiator. When polymerization begins and polymer is generated, it start the precipitation because it is insoluble in solvent.
The feature of Precipitation polymerization is that as it is essentially close to Bulk polymerization and compared with Solution polymerization, the polymerization degree and rate is high but as the heat released by the reaction is absorbed by the solvent, so it is relatively easy to adjust temperature.
Since a polymer simple substance can be obtained and suspension stabilizer or the emulsifier like suspension polymerization or emulsification polymerization will not be used if precipitation polymerization isolates and is dried after polymerization, pure polymer can be obtained. However, this polymerization can be used only for the limited monomer and the combination of a solvent.
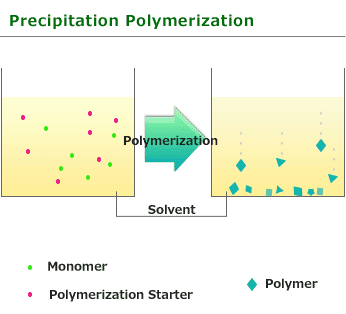